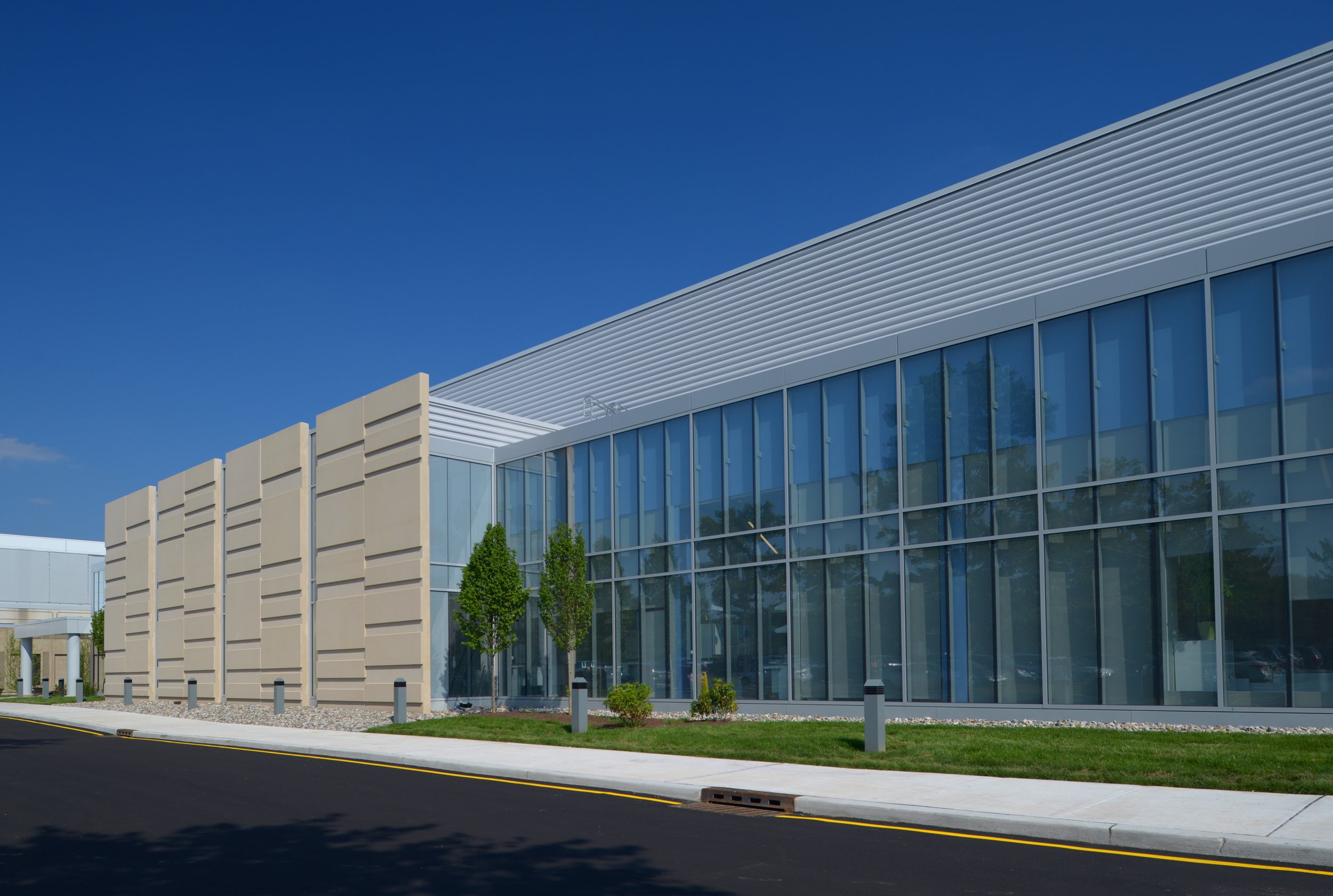
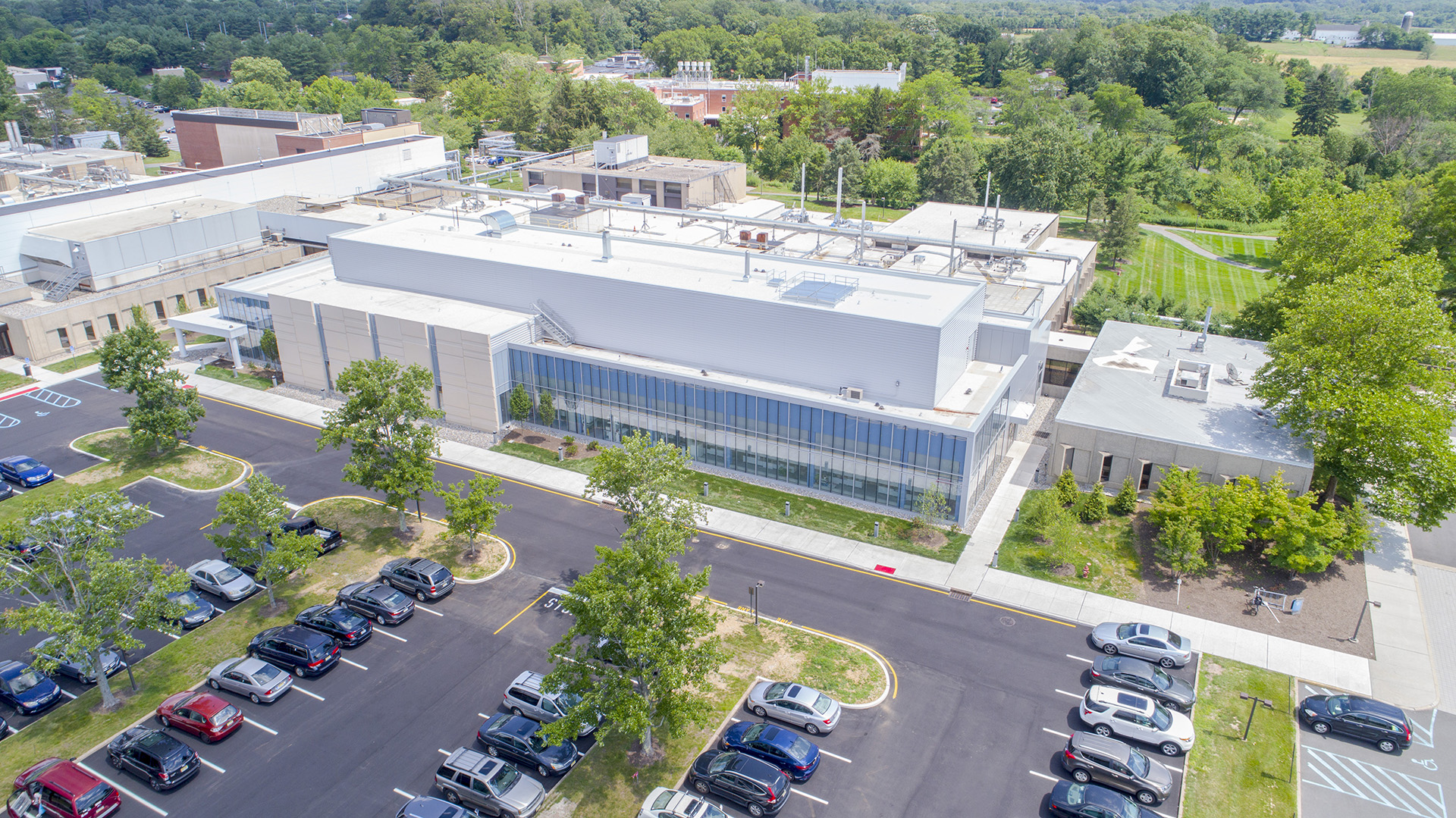
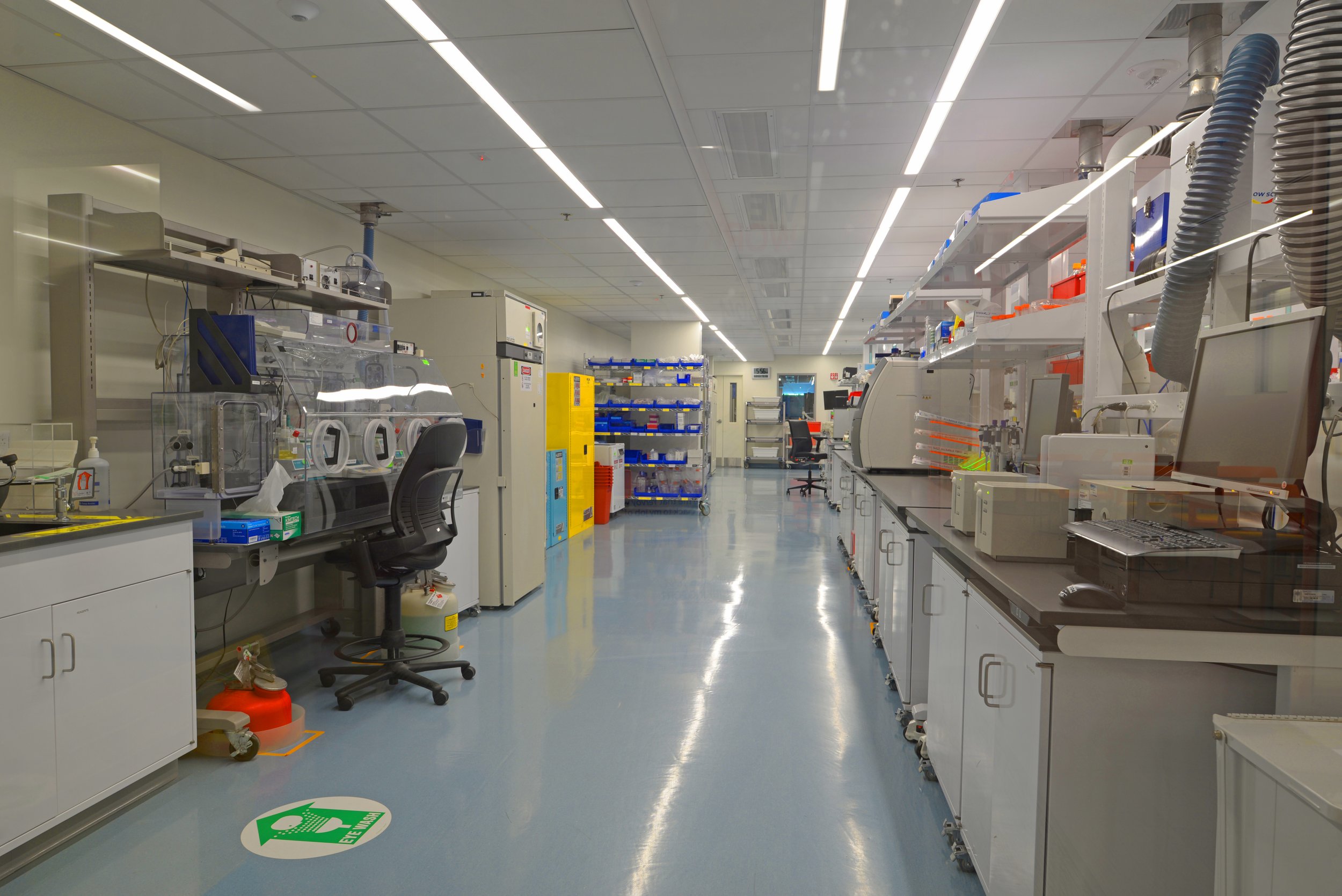
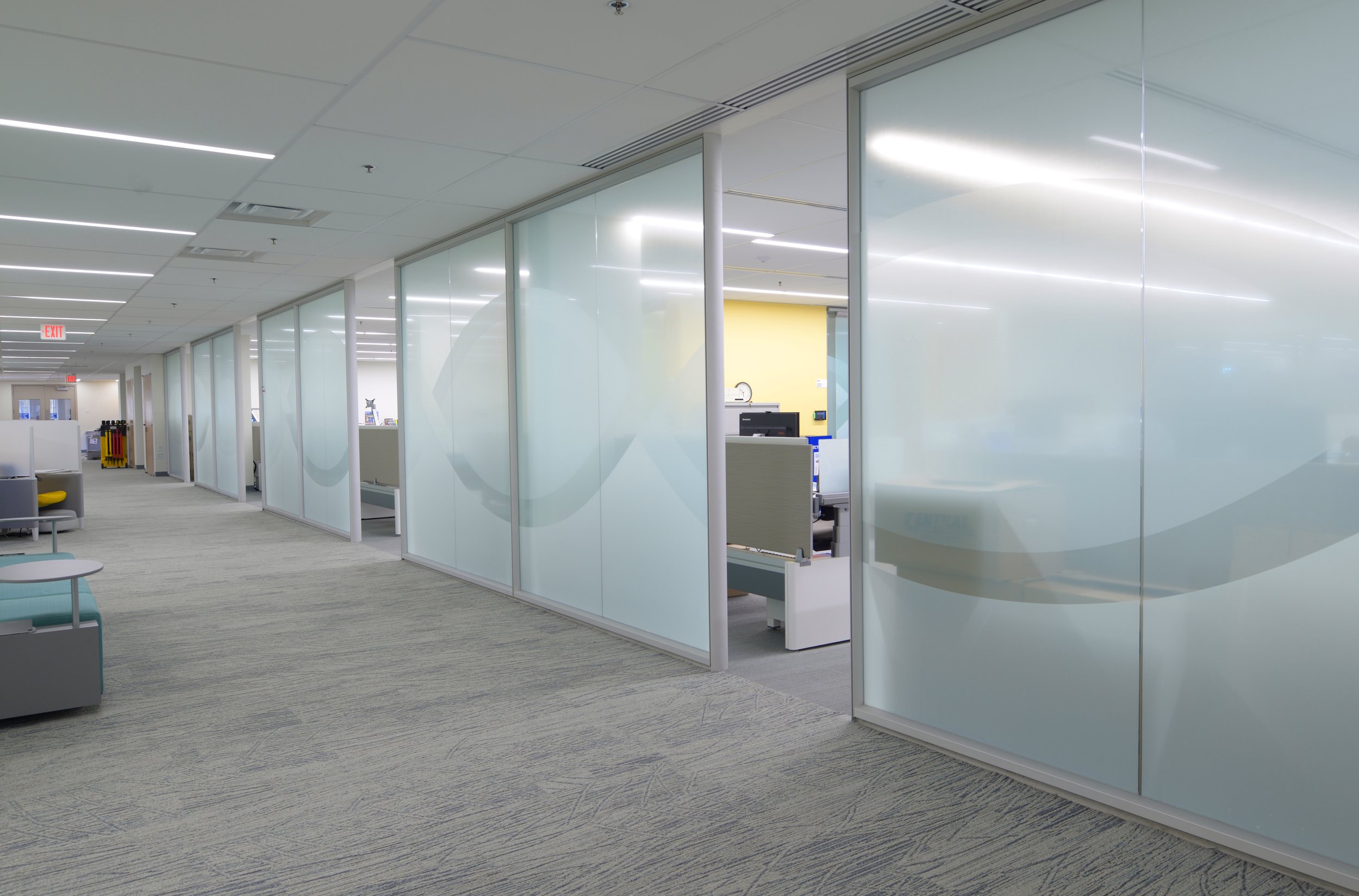

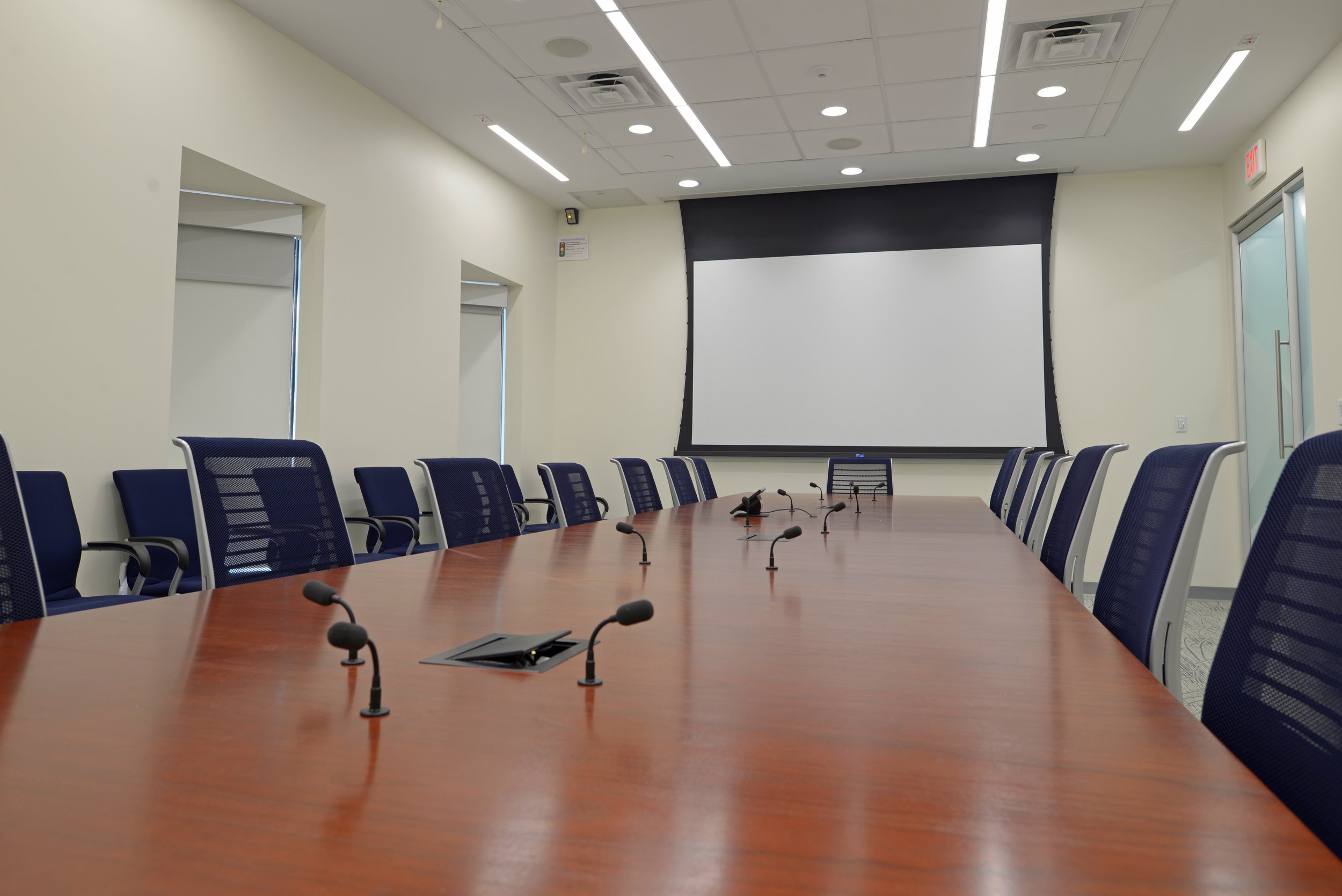
THE OPPORTUNITY
PS&S was asked to provide a design to renovate an existing 1970’s research lab into a state of the art Biologics Development Lab for multiple products. A new building expansion was required along with the renovation. PS&S provided Programming, Local, State & Environmental Permitting, Construction Documents and Construction Support for six phases of construction. Along with architecture, mechanical, electrical, and piping design, PS&S also provided the geotechnical reporting and the structural engineering. The lab also supported Clinical operations which required the design to follow cGMP guidelines.
THE CHALLENGE
The change in the type of work environment from individual labs and offices to an open flexible plan was a shift in the way the client operated. The design process involved user design charrette sessions to fully engage the lab personnel and get the ideas for this change out on the table. Programming efforts investigated shared lab equipment and consolidated similar laboratory functions. A mock up was created for the new lab utility delivery approach and sample furniture was brought to the site to select new office workstation needs. These activities gave the end user the chance to have a voice in the project.
New Robotic equipment was in the program and required future growth. These spaces were designed to be ISO 7 with ISO 5 laminar flow capability.
Separation of the GMP lab, that supported the Clinical Products from the general developmental analytical labs was required to meet cGMP needs. This also included a new cGMP quarantine and wash area. Project was designed to be built in phases that would allow the Clinical Operations to continue without interruption.
THE PS&S SOLUTION
The labs were designed to be an open environment with portable benches and casework. Movable furniture that can be rearranged around one of four standard utility column elements that offered a variety power, gases, data and an exhaust vent options. Ergonomics were considered for safety and the concept of rapid lab reconfiguration. The equipment that supported the Clinical operations, requiring validation was located in the layout to minimize the need to revalidate equipment twice.
Robotic equipment was located within the new building addition, to address the need for new HVAC, high ceiling clearance and the access to the exterior for installation of future robotic equipment.
Open office planning was developed with a variety of alternate seating options, such as Quiet Focus Rooms, Huddle Spaces for 2-3 person conversations, Pantry Spaces and Conference Rooms.