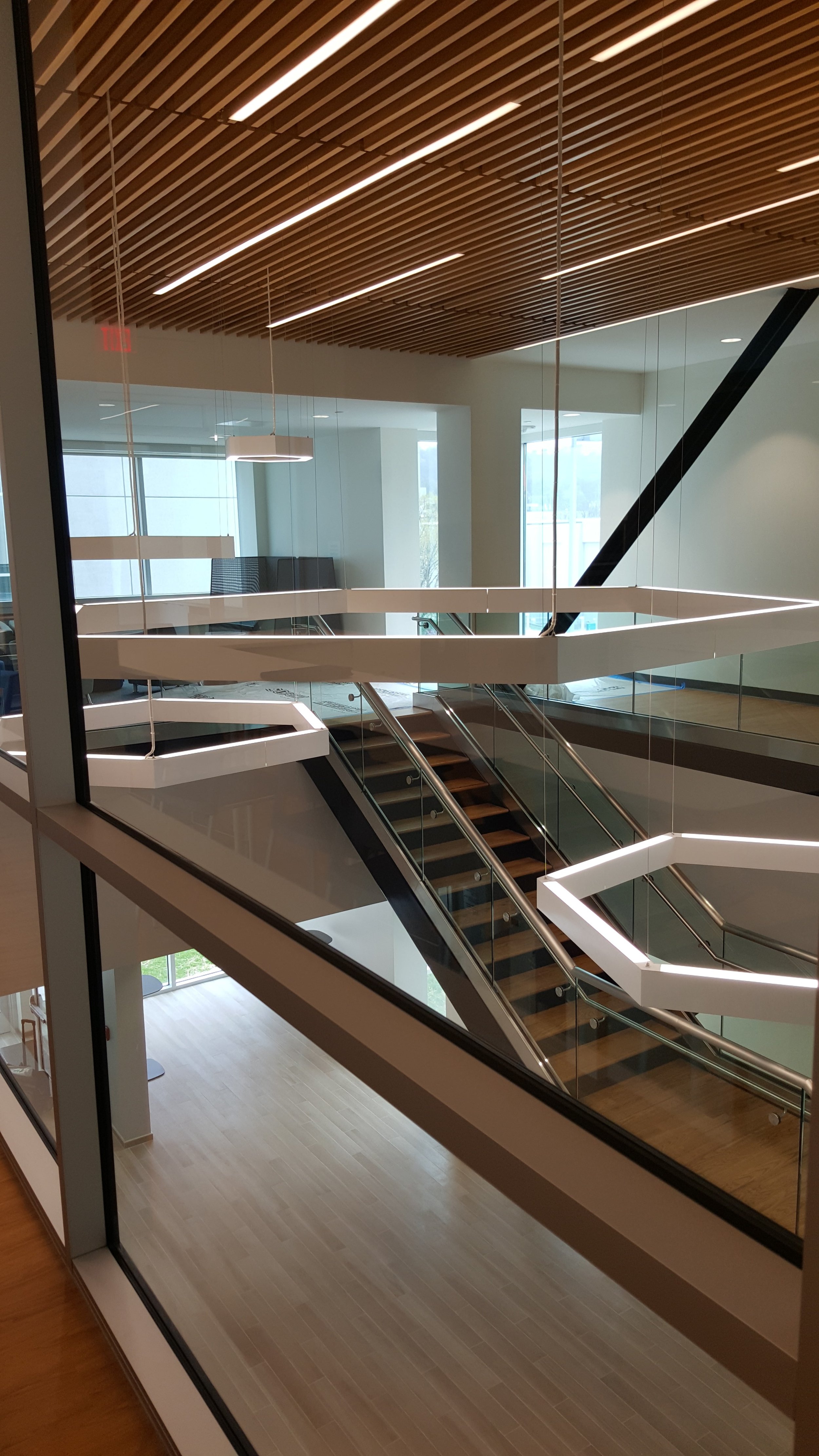
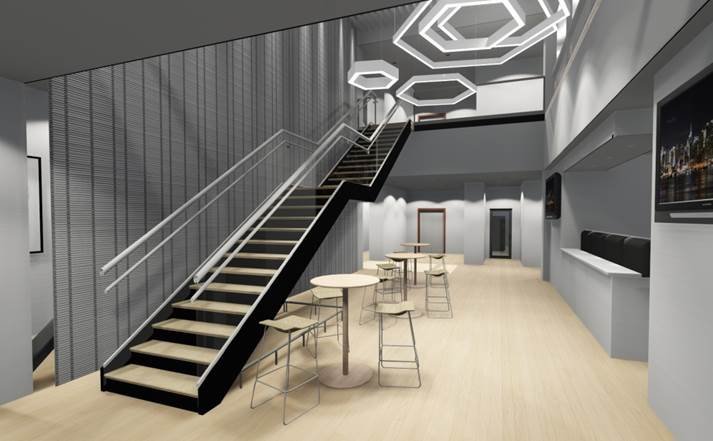
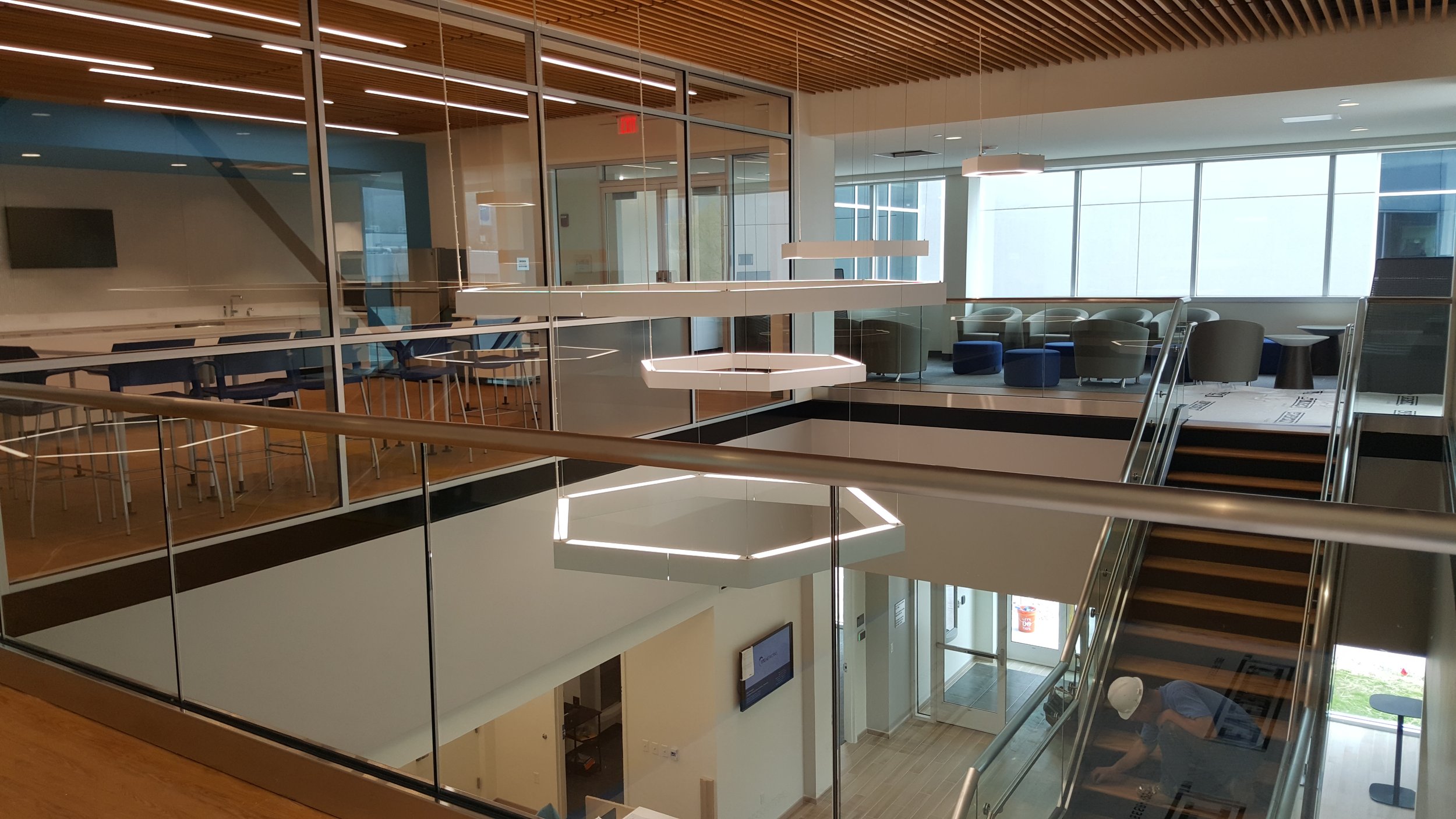
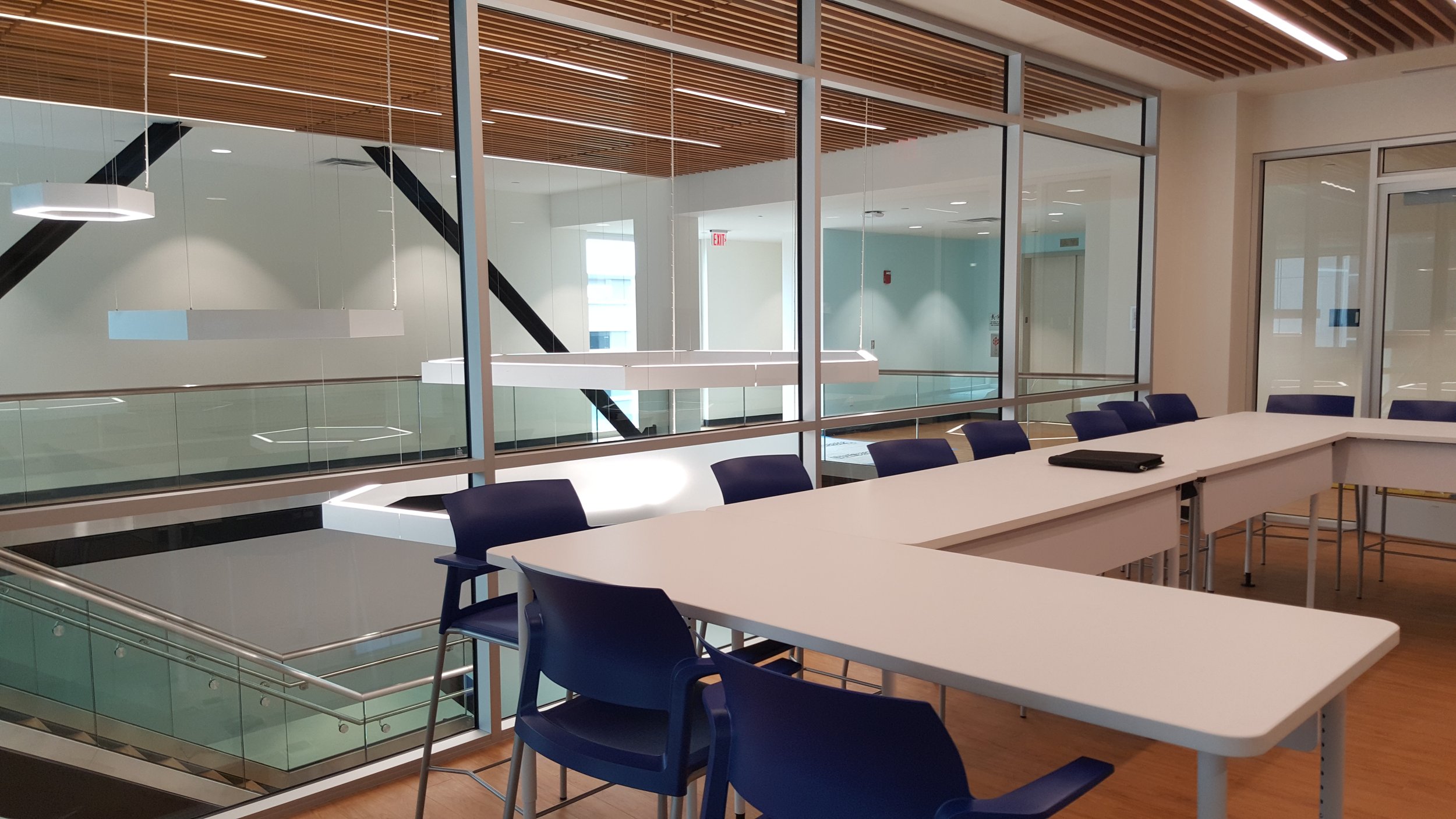
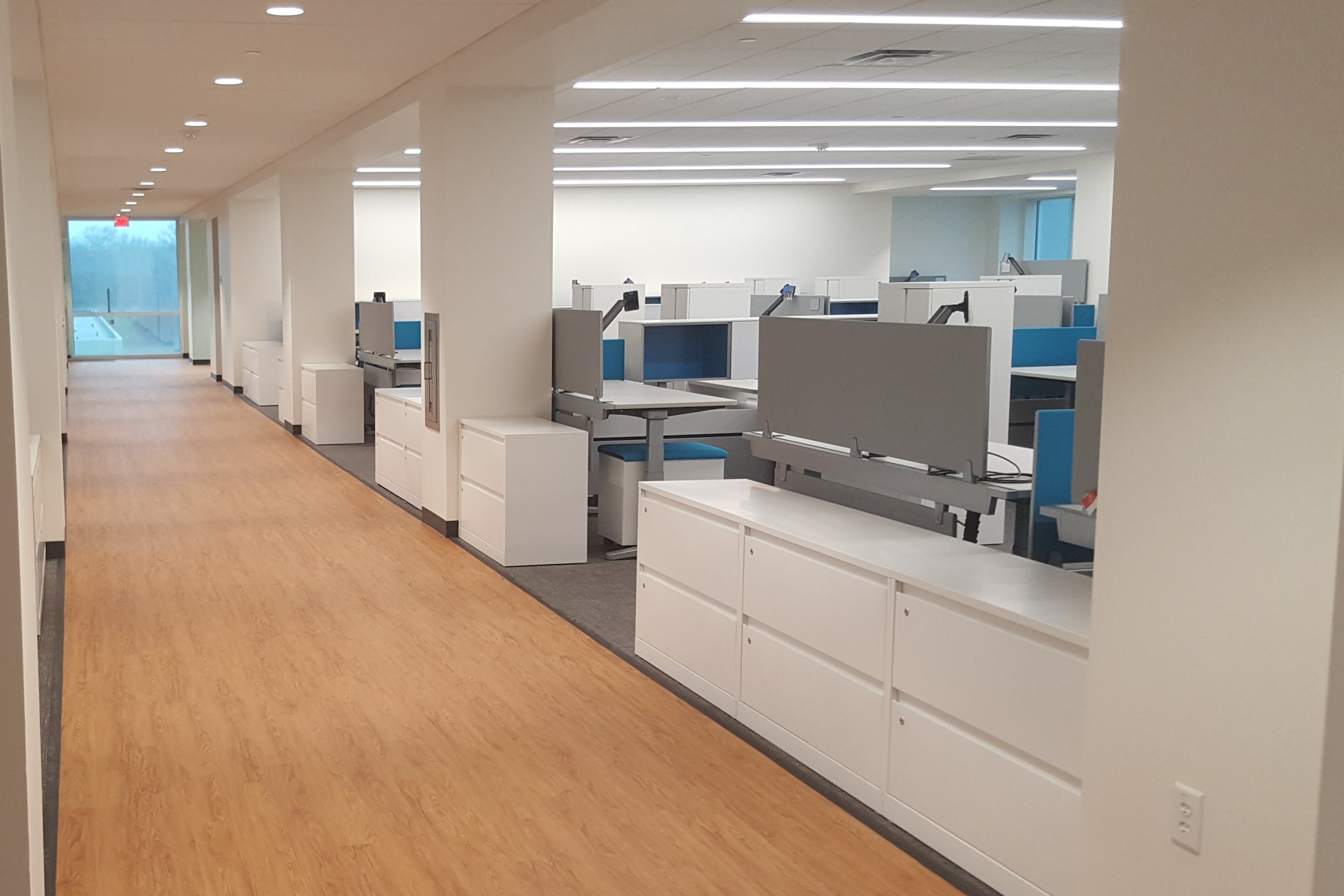
THE OPPORTUNITY
This Health and Nutritional Division of this International Food Company needed full design services for a product technology center to be utilized as a pilot plant. The scope included the renovation of a 192,000 SF four-story building to support product development for the US market. The program consisted of Dry Pilot Plant, Aseptic Pilot Plant, Laboratories for QC, Laboratories for Research, Sensory Testing, Warehousing, Packaging, and support offices.
PS&S provided Architectural, Process, Structural, Mechanical, Electrical, Piping, Plumbing, and Fire Protection engineering services from program through construction administration services. The program was required to be developed with FDA compliant hygienic facility design and align with global client manufacturing capabilities.
THE CHALLENGE
The multiproduct use of a pilot plant is always a challenge. In this design the additional challenge of separating allergenic and non-allergenic products was a material flow exercise. The use of closed Intermediate Bulk Containers IBC’s with split butterfly valves solved dispensing and batch formulation needs. Cleaning of a variety of unknown types of equipment was also a challenge and manual and CIP systems were considered to allow flexibility. The research labs were also required to be flexible to address upcoming new technologies.
There was a need to develop innovative architectural details using standard US building system components to match the parent company’s European-based hygienic standards. PS&S had to modify the existing building utility systems to meet GMP requirements with minimum disruptions to the surrounding occupied campus buildings.
Lastly, an additional challenge was to provide public access to the Sensory Testing space. An interactive, collaborative office environment was required to support the corporate approach to the workspace and therefore the control of odors and public traffic was a major consideration during the design of the workplace.
THE PS&S SOLUTION
In addition to using the IBC’s, the clinical pilot plant was designed to allow the introduction of new large equipment through removable panels in the building shell. Critical utilities were sized and specified to have expandable components added at a later date. The utilities for both the pilot plant and the laboratory adopted a plug and play approach. Movable furniture and utility columns equipped with a variety of power and lab gases were introduced into the plan to allow flexibility.
PS&S provided architectural and engineering interior design services for the project, including coordination with the client’s inhouse experts and process equipment vendors. Revit 3D Building Information Modeling (BIM) was used during design and construction to help visualize, coordinate, and engineer building systems.